Autoclave validation is a critical process in the #pharmaceutical industry, particularly in the #manufacturing of #sterile #medicinal products.
It ensures that the autoclave is functioning correctly and consistently, delivering the desired #sterilization level.
This blog post will delve into the importance of autoclave validation, its role in maintaining product quality and safety, the Good Manufacturing Practice (#GMP) requirements and procedures involved in autoclave #validation, and the important parameters and acceptance criteria during the validation process.
➡ What is Autoclave Validation?
Autoclave validation is a process that verifies and #documents that an autoclave is working within its specified parameters consistently. It involves a series of #tests conducted under defined #conditions to demonstrate that the autoclave can sterilize products #effectively and #reproducibly.
➡ Importance of Autoclave Validation
#️⃣ Ensuring Sterility
✅ The primary purpose of an autoclave is to #sterilize products, eliminating or deactivating potential contaminants such as #bacteria, #viruses, #fungi, and #spores. Validation ensures that the autoclave achieves this goal effectively and consistently, ensuring the #sterility of the final product.
#️⃣ Compliance with Regulatory Standards
✅ Regulatory bodies such as the Food and Drug Administration (#FDA) and the European Medicines Agency (#EMA) require pharmaceutical companies to validate their sterilization processes. Autoclave validation is part of this requirement, ensuring that companies comply with industry standards and regulations.
#️⃣ Quality Assurance
✅ Autoclave validation is a critical component of a company’s #quality assurance program. It helps identify any #deviations or #malfunctions in the autoclave that could compromise the sterility of the product. By ensuring the autoclave operates within its specified parameters, companies can #assure the #quality and #safety of their products.
#️⃣ Cost-Efficiency
✅ While autoclave validation may seem like an added expense, it can save companies money in the long run. A malfunctioning autoclave can lead to #product recalls, #regulatory fines, and damage to a company’s reputation. By validating their autoclaves, companies can avoid these costly issues.
➡ Key steps & GMP Requirements and Procedures for Autoclave Validation
✅ Installation Qualification (#IQ)
✅ Operational Qualification (#OQ)
✅ Performance Qualification (#PQ)
✅ Routine Re-Qualification
➡ Important Parameters and Acceptance Criteria
During the validation process, several important parameters (#Temperature, #Pressure, #Time, #Steamquality) are monitored and must meet specific acceptance criteria.
By adhering to GMP requirements & procedures for autoclave validation, & by monitoring and meeting the important parameters & acceptance criteria during the validation process, companies can ensure the safety & efficacy of their products, ultimately protecting public health.
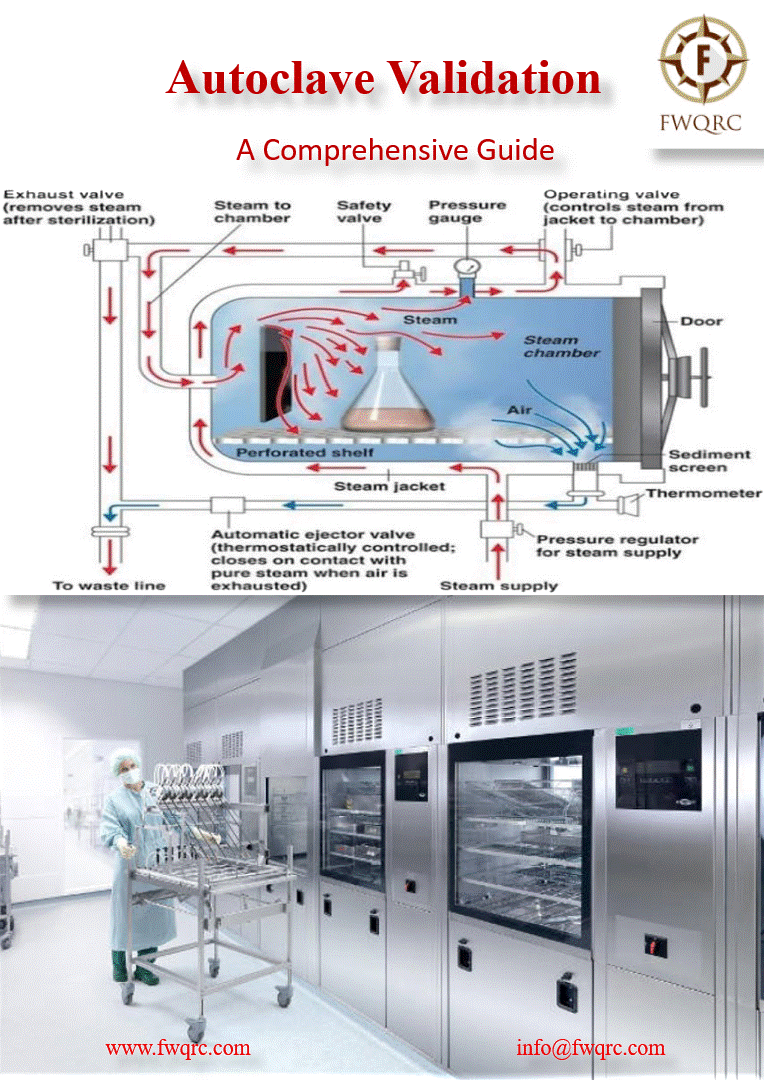